The Best Stainless Steel Tube Supplier in China
With many years of experience in stainless steel production, we have signed cooperation with many steel companies. These steel companies are steel companies with the best quality in China, such as Baosteel and TISCO. We provide you with stainless steel products produced in China with very competitive stainless steel prices and quality. We provide the best stainless steel solutions for the stainless steel raw material supplies industry in various industries. We are a flexible stainless steel company. We have rich experience in stainless steel production and procurement to manage our products and mix stainless steel products purchased from other high-quality stainless steel companies.
Myriad has long provided cold-rolled stainless steel coils for stainless steel tube manufacturers. At the same time, we also provide cold-rolled stainless steel coils for the stainless steel tube factory to process us into the stainless steel tubes you need. Yaoyi can meet all your purchasing needs for stainless steel pipes. As your reliable partner and procurement agent, we will provide support for your stainless steel pipe procurement. Ask now for a better quote for stainless steel pipes.
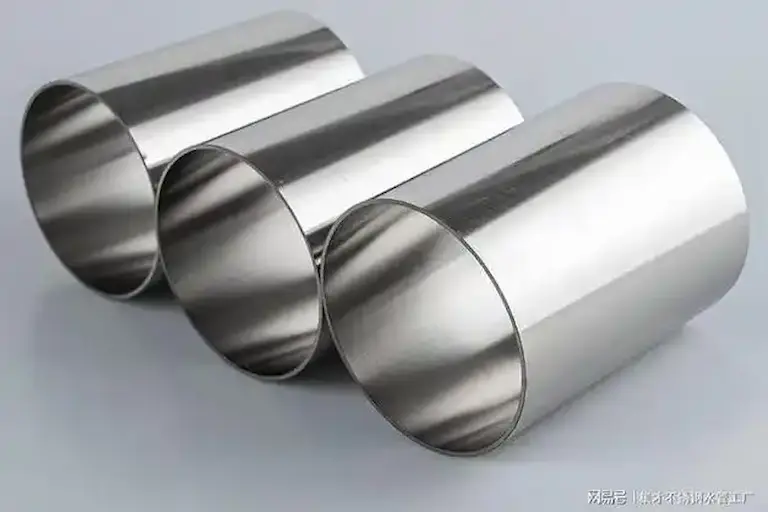
Get BEST Stainless Steel Strips From China
304 Stainless Steel Strip
301 Stainless Steel Strip
316 Stainless Steel Strip
316L Stainless Steel Strip
201 Stainless Steel Strip
J1 stainless steel coil strip
J3 stainless steel coil strip
J4 stainless steel coil strip
Material Testing After You Place An Stainless Steel Ties Order
Hardness Testing
Ingredient detection
Tensile Strength Test
Table of Contents
How to weld stainless steel tube?
Austenitic stainless steel has excellent weldability, toughness, and corrosion resistance, as well as good machining properties. In the processing and manufacturing of stainless steel pipes, welding is an indispensable machining technology. With the increasing application of stainless steel pipes, the variety, mechanical properties, and quality requirements of related welded parts are constantly increasing, so the requirements for welding methods and processes are gradually increasing.
First of all: work preparation before welding.
1.1 Preparation of stainless steel pipe
In order to ensure the welding quality, the level of the end face of the stainless steel pipe cannot be processed with an oxygen-acetylene gas cutter. According to the form of the plate thickness, the groove is processed by machining, plasma arc cutting, or carbon arc gouging. To avoid splash metal damage, the lime powder should be applied to both sides of the groove when using carbon arc air gouging and manual arc welding.
1.2 Grinding grooves and assembly tack welding
In order to ensure the shape of the weld at the root of the pipe and meet its performance, this process selects argon tungsten arc welding. When opening the groove, if the pipe wall is larger than 4mm, the pipe should have a V-shaped groove. When the wall thickness is less than 4mm, you can choose Do not to open the groove. Here, an angle grinder is used to grind the grooves of the two pipes, and the two sides of the grooves are polished 20 to 30mm to expose the metallic luster. As stainless steel is prone to intergranular corrosion, a smaller welding current is required.
Therefore, the penetration depth is small, so the blunt edge of the bevel is smaller than that of carbon steel, about 0 ~ 0.5mm, and there is generally no blunt edge in production. The bevel angle is larger than that of carbon steel, about 65°~70°.
1.3 Clean up before welding
In order to ensure the quality of the welded joints and welds, the welds and electrodes should be cleaned before welding. The weldment groove must be cleaned within 20-30mm on both sides of the groove. If there are oil stains, organic solvents such as alcohol or acetone can be used. Wipe. To use
For higher parts, in order to prevent metal splashes from damaging the surface of the workpiece during welding, paste paddles prepared with white powder are applied to the appropriate range on both sides of the weld.
1.4 Surface protection
In order to ensure the quality of the welding workpiece, care should be taken to avoid damaging the surface of the weldment as much as possible during the pre-wedding preparation and welding process, otherwise, the corrosion resistance of the stainless steel welded product will decrease. For example, when moving the weldment, be careful not to scratch the surface of the steel with some sharp tools. When starting the arc, you must start the arc on the arc ignition plate as required, and you cannot start the arc at will.
1.5 Welding equipment and materials
ZX7-400ST inverter type argon arc welding machine (Ⅲ); argon cylinder and argon flow regulator; cerium tungsten electrode (diameter Φ2.5); air-cooled welding gun; welding material: stainless steel wire ER347(H08Cr20Ni10Nb)Φ2. 5; Angle grinder, cutting machine, and other auxiliary equipment.
The Second: the welding process
2.1 Determine the welding position
The welding consumables and welding quality requirements of the tack welding and the formal weld must be the same, and the height and width and the reverse shape must be consistent with the formal weld. If there is an apparent defect on the tack weld, it should be polished off. Generally, the tack weld should be no less than 3 points, and the tack weld length is about 10mm.
2.2 Welding
Adopt the tungsten argon arc welding process. This process is three-layer but three-pass welding. In order to ensure the quality of the weld, we should continuously fill the tube with argon during welding, and ensure that both ends of the tube are sealed, and use large-diameter partial argon for welding of stainless steel tubes. As austenitic stainless steel has better plasticity, the tendency of cold cracks is small, so in general, there is no need to preheat before welding. When performing multi-layer and multi-pass welding, in order to avoid some defects due to an excessively high temperature between the weld passes, the weld seam needs to be cooled after welding one layer before welding the next layer. For some weldments with relatively large rigidity, it is best to preheat before welding in order to avoid welding cracks. In order to prevent the temperature of the welding joint from being too high, the welding current should be 10%-20% lower than that of carbon steel welding. The welding method adopts short arc fast welding, straight-line transportation, and the arc starting and ending times are reduced as much as possible during the welding process. , To avoid repeated heating of the weld. To ensure that the surface of the weldment is intact, collision damage should be avoided, especially to avoid local burns caused by arc ignition on the surface of the weldment. Welders should not start the arc at the non-welded seam to avoid damage to the base material and cause corrosion. The interlayer temperature must be controlled during the welding process. The interlayer temperature of austenitic steel is less than 60℃. This welding adopts the process of single-sided welding and double-sided forming. In the welding process, try to use the bottom welding position. Pay attention to the weld pool during welding, and promptly remove welding defects such as cracks, pores, and slag inclusions. In the welding process, the interruption time is too long, and the end of the welding wire may be oxidized. Therefore, when the welding is continued, remove the end of the welding wire. When the arc is extinguished at the end of welding, pay attention to the protective effect of the lagging gas on the weld.
At last: heat treatment after welding
After austenitic stainless steel is welded, post-weld heat treatment is generally not required. If the performance requirements of the welded workpiece are high, low-temperature, medium-temperature, or high-temperature post-weld heat treatment can be selected according to the actual situation.
Study Stainless Steel Technical Made Simple: A Step-by-Step Guide
How to calculate metal weight?
Steel tube (including seamless steel pipe and welded steel pipe (kg/m)
W= 0.02466 * S (D – S)
D = outer diameter
S = wall thickness
For example: For seamless steel pipes with an outer diameter of 60 mm and a wall thickness of 4 mm, find the weight per m.
Weight per m = 0.02466 * 4 * (60 –4)=5.52kg
Simple calculation formula for stainless steel weight:
Weight per square meter of stainless steel sheet (kg)= specific gravity * thickness (mm) * width (mm) * length (m)
stainless steel weight per meter (kg) = diameter (mm)*diameter (mm)* (nickel stainless: 0.00623; chromium stainless: 0.00609)
Stainless steel square rectangle weight per meter formula:
Stainless steel square rectangle weight per meter (kg)=(perimeter of nozzle/3.14-actual thickness)*actual thickness*0.02491
For example:Calculate the weight of a 4-meter-long yaoyi 304 stainless steel square pipe: 40*15*0.62.
[(40+15)*2/3.14-0.62]*0.62*0.0249*4=2.125kg
FOCUSED ON THE 0.03 ~ 0.05 mm Stainless Steel Foil
What are the requirements for the packaging of stainless steel tubes?

Through a complete production management system, we can provide you with excellent quality and cost-effective stainless steel pipes to your satisfaction.
To ensure that the quality of our products are the same when they leave the factory and when you receive them, we provide you with the best product packaging.
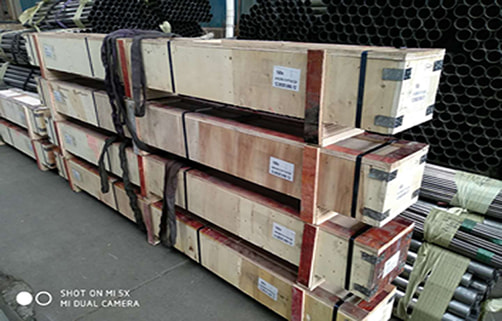
First of all, pack your products in good condition during transportation, loading, and unloading. To achieve this effect, our packaging needs to carry shock-absorbing and shock-proof measures.
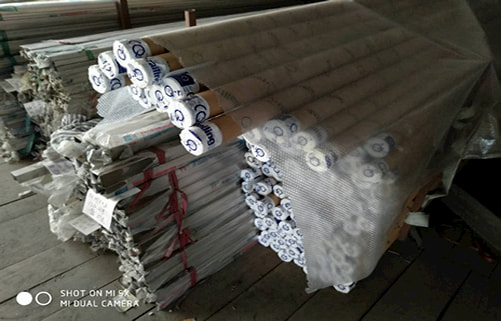
Secondly, to adapt to the large number of gelatinous, unloading, and long-term open-air problems faced by the land or sea during the transportation process, the stainless steel tube packaging we provide you includes moisture, sun, mildew, rust, and Corrosion protection measures.
1.1 There is a label (mark) on the outer box of the stainless steel pipe, indicating the contract number and product name. If it is a matching part, it needs to indicate the serial number that should not be seen in the assembly drawing. At the same time, the label must have the box number/part number; gross weight/net weight (kg); volume (length × width × height, expressed in millimeters); × height, expressed in millimeters); production plant;
1.2 At the same time, we will carry the inspection report of the stainless steel pipe and the certificate of qualified quality.
1.3 The loose and scattered parts of various equipment should be packed in good packaging methods, packed in boxes of appropriate size, and shipped as whole vehicles as possible to reduce transportation costs.
1.4 To ensure that the surface of the stainless steel tube will not be scratched during the movement and long-distance movement of the stainless steel tube, which will affect the appearance, we will cover the stainless steel tube with a packaging film bag.
1.5 The stainless steel pipes of a single product specification are individually boxed, and the boxes are numbered consecutively, and the order of the box numbers is always consistent during all shipments.
1.6 To further protect the appearance of the stainless steel pipe. While using our packaging film bag to cover the stainless steel tube, each stainless steel tube is also wrapped in a paper tube (see picture).
4 Common Methods for Welding Stainless Steel Pipe
How to cut stainless steel tubing?
The first is grinding wheel cutting; this is currently the most commonly used cutting method. As the name suggests, the grinding wheel is used as a cutting tool to cut stainless steel on it. It is also the cheapest cutting method, but since it will produce many burrs after cutting, a deburring process is required in the later stage. Some manufacturers have no requirements for burrs, and this method is the simplest and lowest cost method.
The second method is wire cutting, which is to let the stainless steel capillary tube cut the wire on the wire cutting machine, but this method will cause discoloration of the nozzle. In the case of manufacturers with stricter requirements, it needs to go through post-processing, such as polishing and grinding. deal with.
The third method is a metal circular saw cutting; the product cut by this cutting method is very good, and several pieces can be cut together, the efficiency is also very good, but the disadvantage is that the chips are easy to stick to the tool, so choose the saw The film must be very careful.
The fourth method is cutting with a hob chipless pipe cutting machine. This cutting method has a very good cut. However, this method is not suitable for cutting Bobby’s stainless steel pipes. It is very easy to tear and the nozzle will be deformed.
How many surface treatment methods are there for stainless steel tubes?
First of all, when most of the stainless steel pipes leave the factory, they are the same as most of the products we see in our lives. The surface is polished, showing a silver-white metallic luster, and is very flat and smooth. This is what everyone often says Noodle tube.
The Second, for those factories that make high-end products, ordinary bright-faced tubes cannot meet the product requirements, so on this basis, more demanding surface treatment methods are derived. Mirror tube, the surface of this material has the advantages of high brightness and strong aesthetics, but the disadvantage is that it is easy to scratch and requires caution during use.
The Third, as the processing technology of stainless steel pipes continues to improve, there are many kinds of processed pipes on the market. Among them, we often see some very fine lines on the surface of some pipes, which can be seen and are very beautiful. This is one of the most common processing techniques for pipes-wire drawing.
The Finally, with the development of society, people’s vision has become increasingly critical. In the past, as long as the surface of the pipe is smooth and flat, what is required is not just that simple. People have begun to chase the processing technology of pipes for better visual effects and a more beautiful appearance. Among them, the brushed pipes are the most common, and their texture All kinds. We usually have the following types: straight wire tube, round wire tube, snow pattern, nylon pattern. The most common and popular one is the straight thread pattern. The straight thread pattern is an uninterrupted pattern from top to bottom. Generally, a fixed drawing machine can be used to move back and forth. The relative cost of the straight thread pattern is also the lowest among these kinds of patterns.
In general, the common surface treatment methods for pipes are roughly medium, embryonic tubes (also called black tubes), shiny tubes, high-standard mirror tubes, and brushed surfaces (commonly known as matte)
Comparison of Stainless Steel Standards in Different Countries
What is stainless steel tubes used to?
Produced by 312/A312M -03 welded austenitic stainless steel pipe standard.
Suitable for austenitic stainless steel seamless steel pipes and straight seam steel pipes used in high temperature and general corrosive environments.
Uses petrochemical, papermaking, winemaking, gas, steam, tap water, sewage treatment, and other projects.
Specification requirements:
Outer diameter: Φ21.34, 26.67, 33.4, 42.16, 48.26, 60.33, 73.03, 88.9, 101.6, 114.3, 141.3, 168.28, 219.08
Thickness: 1.65-8.18 mm
Material: 304 stainless steel, 304L stainless steel, 316L stainless steel
According to JIS G3459 welding austenitic stainless steel pipe standard, it produces austenitic stainless steel seamless steel pipe and straight seam steel pipe suitable for use in high temperature and general corrosion environment.
Uses petrochemical, papermaking, winemaking, gas, steam, tap water, sewage treatment, and other projects.
Outer diameter: Φ21.7, 27.2, 34, 42.7, 48.6, 60.5, 76.3, 89.1, 101.6, 114.3, 139.8, 165.2, 216.3
Thickness: 1.65-8.2mm
Wall thickness tolerance: less than 2mm±0.2mm, more than 2mm±10%
Material: 304 stainless steel, 304L stainless steel, 316L stainless steel
According to ASTM A554 welding austenitic stainless steel standard, it is suitable for use in various machinery manufacturing.
Outer diameter: Φ19.1, 22.2, 25.4, 28.6, 31.8, 38.1, 48.6, 50.8, 60.3, 63.5, 76.2, 88.9, 101.6, 114.3
Thickness: 0.7-3.0mm Thickness tolerance: ±10%
Material: 304 stainless steel, 304L stainless steel, 316L stainless steel
According to DIN 17457 welding austenitic stainless steel pipe standard production, suitable for austenitic stainless steel seamless steel pipe and straight seam steel pipe used in high temperature and general corrosive environment.
Uses petrochemical, papermaking, winemaking, gas, steam, tap water, sewage treatment, and other projects.
Outer diameter: Φ21.3, 26.9, 33.7, 42.4, 48.3, 60.3, 76.1, 88.9, 114.3
Thickness: 1.5-4.0mm
Material: 304 stainless steel, 304L stainless steel, 316L stainless steel
Produced according to A249/A249M-02 standard
Purpose: Standard for austenitic welded steel for boilers, superheaters, heat exchangers, and condenser tubes
Outer diameter: Φ16, 19, 20, 22, 25, 32, 38, etc.
Thickness: 0.8-10mm
Wall thickness tolerance: ±10%
Material: 304 stainless steel, 304L stainless steel, 316L stainless steel
What is sanitary stainless steel tubes?
Sanitary stainless steel pipes have a variety of different strength and weight ratios, and the surface finish of different grades and specifications of sanitary stainless steel pipes can meet different customer needs. It has the characteristics of high practicality, long service life, and low maintenance cost. Because sanitary stainless steel pipes are easy to shape and have a good appearance, they are used by many architects. Sanitary stainless steel pipes are also called seamless stainless steel pipes. They are made of solid stainless steel pipes or steel ingots, and then they are hot rolled and cold rolled. The specification of sanitary stainless steel pipe (seamless stainless steel pipe) uses outer diameter * wall thickness (mm). Sanitary stainless steel pipe is cross-section steel with high-cost performance. It is widely used in decoration or industry. Common products are 201 stainless steel pipe, 304 stainless steel pipe, 316 stainless steel pipe. But you need to clearly explain to the factory whether you are purchasing stainless steel welded pipe or stainless steel seamless pipe when purchasing.
How to weld stainless steel seampless pipe?
First of all, the choice of stainless steel seamless pipe.
Stainless steel tubes (seamless tubes) can generally be divided into bright annealed BA) tubes and electropolished (EP) tubes. The BA tube is heated by argon filling, and the EP tube is processed by electrolytic grinding. The flatness and flatness of the EP tube are better than that of the BA tube, and its inner and outer surfaces are very bright. According to the requirements of the design documents, a project uses two grades of EP sanitary stainless steel pipes of 304 and 316L, with nominal diameter (DN) of 20-200 mm and a wall thickness of 2 mm. The pipes are made of nickel with good passivation properties. It has good corrosion resistance in both oxidizing media and reducing media.
The Second, self-fusion welding technology.
The clean pipeline adopting self-fusion welding technology can not only meet the requirements of conventional industrial pipelines for welding seams, but also ensure that the inner and outer surfaces of the pipeline are not polluted during welding, and the inner and outer surfaces of the welding seams remain bright and shiny with the base material. The degree is basically the same. The welding seam and the base metal are smoothly transitioned, and the internal and external heights of the pipeline are small, and they are basically flush with the base metal. Moreover, clean pipelines are mostly operated in clean rooms. During the operation, the operating environment must be guaranteed to be free from pollution and smoke-free and dust-free. Therefore, self-fusion welding is the most suitable welding method. The diameter of the stainless steel clean pipeline is small, generally less than DN 200 mm. The welding seam requires single-sided welding and double-sided forming. The on-site process pipelines should be arranged in rows and the spacing should be wide and even. The welding work can be completed by an automatic welding machine. The automatic welding machine is composed of 4 parts: welding host, display screen, controller, and welding gun. When using this automatic welding machine, the pipes can be assembled without grooves and no gaps. The welded joints are formed through the self-fusion of the base material, which can effectively avoid contamination in the pipes. Self-fusion welding machine implements full-program operation. When compiling the welding program, the joint end surface can be divided into 4 sectors according to the outer diameter of the pipe (that is, divided into 4 levels). Each welding program can be divided into up to 100 levels. Each level can be set according to actual welding requirements. The welding procedure can meet the welding requirements and form a dynamic mode to ensure the welding quality, and the pulse current can ensure that the welding ripple is very uniform and small, and the weld surface remains smooth.
The welding gun is the biggest difference between the automatic welding machine and other welding machines. It is composed of a protective cover, a tungsten needle, and an argon gas tube. When in use, the protective cover is buckled on the pipe welding port, the argon gas pipe is filled with argon, and the tungsten needle starts circumferential welding around the welding port along the guide rail in the protective cover.
At last, welding parameter setting
Use argon with a purity of 99.99% or more as the protective gas, because argon can effectively isolate the surrounding air and it does not react with metals. Also, in the welding process of argon tungsten arc welding, the arc also has the function of automatically removing the oxide film on the surface of the workpiece, so it can successfully weld stainless steel and alloys that are easy to be oxidized, nitrided, and chemically active. In theory, the greater the gas flow rate, the stronger the protective layer’s ability to resist the influence of air. However, in practice, it has been found that when the gas flow rate is too large, the protective layer will flow irregularly, entrap the air, and affect the protective effect. The quality of the weld, so the appropriate argon flow should be selected according to the actual situation during welding. Considering that the project is mostly operated indoors, the argon flow rate is generally adjusted to about 10 L/min. The welding process of stainless steel clean pipe can be divided into prefabrication preparation stage, welding.
Connection stage and post-welding stage. In the prefabrication stage, first, remove the clean tube from the plastic film, measure the used length, cut and level the nozzle with a flat-nozzle machine. In the welding stage, fix the cut clean pipe on the bracket according to the construction drawings and fill the nozzle with argon gas, then clamp the welding torch to the butt nozzle, and set the welding parameters on the self-fusion welding machine, including welding current, welding speed, and argon filling volume, etc., and test the sample tube, optimize the welding parameters, and finally start welding. In the post-welding stage, the weld seam is polished, the clean pipe is pressure-tested, and the pipeline is inspected with a radiographic inspection. Finally, the installation is completed.
How to Remove The Oxide Scale on The Surface of Stainless Steel Casting Billet?