How to Choose the Best Make Stainless Steel Sink Material?
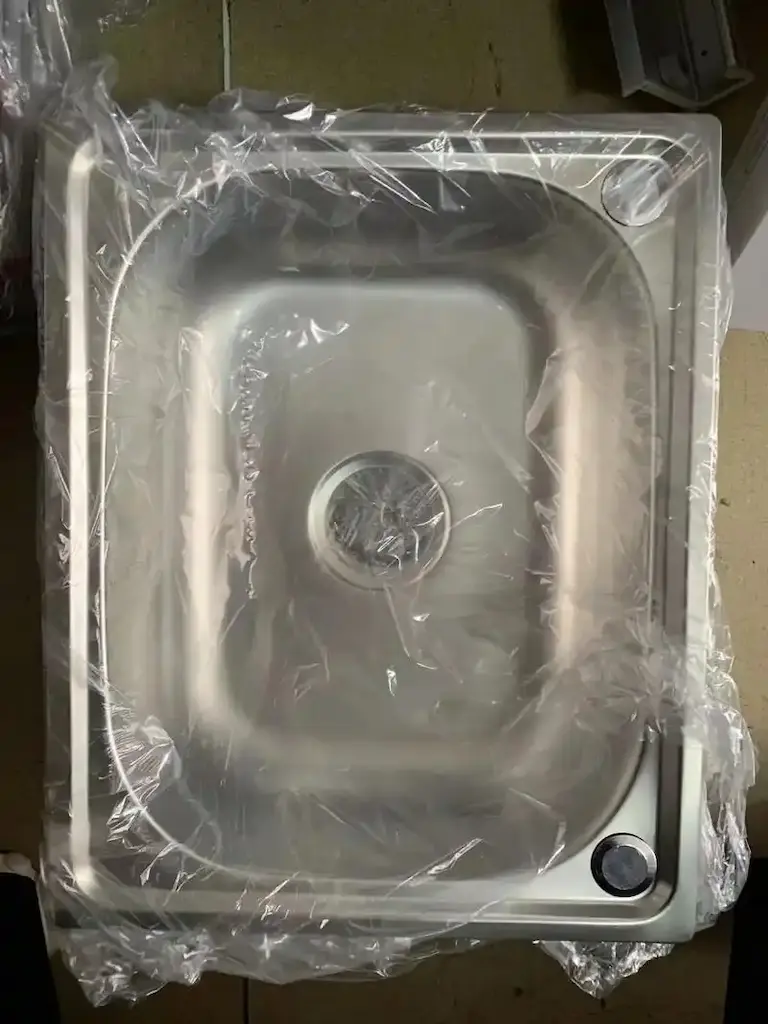
The influence of the radius of the die fillet, the crimping force and the friction factor on the wrinkling problem of SS304 stainless steel sink material during the deep drawing process was investigated by orthogonal test method. The orthogonal test scheme was verified by the finite element analysis software Dynaform, and the relationship between the maximum thickness increase rate and three molding influencing factors, such as die radius, crimp force and friction factor, was investigated.
Based on the optimized results, the mold structure design was improved to solve the molding problem of SS304 stainless steel sink material.
The forming quality of the deep-drawn parts is closely related to the process parameters in the process of deep-drawn forming, which mainly include the radius of concave die, radius of convex die, crimping force, friction factor, gap between convex and concave dies, lubricant, etc. These process conditions can more or less affect the forming quality level of the box-shaped parts. Because of the difference in size of each process parameter setting, it is assumed that the workload is huge to verify all process parameter settings for all factors. The orthogonal test method can effectively screen the influencing factors and the corresponding process parameters and reduce the number of invalid tests.
By performing the molding simulation of SS304 stainless steel sink through the finite element analysis software Dynaform and analyzing and organizing the test data, the suitable process parameters can be found.
How to Make Stainless Steel Sink?
The SS304 stainless steel sink was modeled using UG to form a 3D model, as shown in Figure 1. In the actual production, factors such as crimping force, friction factor, press parameters, die parameters, lubrication conditions, etc. can affect the sink forming quality and cause forming problems.
After reviewing the relevant information and performing relevant molding calculations, it is known that the part can be formed in one press. Among them: the radius of the corner of the convex die is the radius of the inner bottom corner of the part; the press stamping speed and other settings are related to the selection of the press model, which is basically fixed.
Therefore, in actual production, the crimping force, lubrication conditions and die parameters are changed to improve the quality of deep-drawing forming. Therefore, the influence factors of orthogonal test mainly adopt the radius of concave die fillet, crimping force and friction factor.
Radius of concave die
SS304 stainless steel sink material concave die fillet is an important parameter that affects the flow of sheet material. When the plate material flows into the concave die, it will be affected by the bending resistance at the corner of the die, the smaller the corner, the greater the bending resistance, which will lead to the increase of tensile stress in the radial direction of the plate material, and the increase of radial tensile stress will lead to the pulling and cracking phenomenon in the weak part of the bottom corner and side wall intersection. When the angle of the concave die is larger, the material flow into the concave die becomes easy, which will lead to the weakening of the pressure material at the corner of the concave die, and the material will be gathered and extruded, and the wrinkling problem will become prominent.
As we can see from the relevant data, the radius of concave die fillet is usually taken from 4t to 8t [11] (t is the thickness of sheet material). Considering the part’s own characteristics, the four levels of concave die fillet radius are set to 5, 6, 7 and 8 mm respectively.
Friction factor
The friction factor in actual stamping is usually achieved by changing the surface roughness of the die or the surface roughness of the sheet, such as applying lubricating oil, graphite, etc. In the simulation process using Dyanform, the actual friction conditions are usually simulated by changing the friction factor. The structural characteristics of the part indicate that the part is formed as a simple symmetrical deep drawing, and the friction conditions can be set to be the same for all parts of the mold in contact with the sheet. Therefore, the four levels of the friction factor are set to 0.05, 0.10, 0.15 and 0.20 respectively.
Crimping force
Design of the orthogonal test scheme
The factors and levels for the design of this orthogonal test program are shown in Table 1. Where: R is the radius of concave die fillet; C is the friction factor; F is the crimping force.
Radius of concave die
Horizontal |
Concave die fillet radius R/mm |
Friction factor C |
Crimping force F/kN |
1 |
5 |
0.05 |
20 |
2 |
6 |
0.1 |
30 |
3 |
7 |
0.15 |
40 |
4 |
8 |
0.2 |
50 |
Experimental scheme and optimized parameters
Results of orthogonal test
Without considering the interaction between factors, the levels of three factors, such as concave die fillet radius, friction factor and crimping force, were arranged into the orthogonal test. The index for judging whether defects arise after forming of stainless steel sink material is the maximum thickening rate. If the maximum local thickening rate of the sheet exceeds 20%, the risk of wrinkling of the part will be greatly increased.
Analysis of results
According to the results of the orthogonal test, the trend of the maximum thickening rate with the radius of concave die fillet, friction factor and crimping force is plotted.
With the increase of friction factor, the maximum thickness increase rate decreases, which indicates that the increase of friction factor can significantly reduce the risk of wrinkling; with the increase of die radius, the maximum thickness increase rate slightly, but the trend is not obvious, which indicates that the increase of die angle will increase the risk of wrinkling, but it is not significant;
At the same time, the increase of the crimping force also significantly reduces the plate thickening rate, which indicates that the risk of destabilization and wrinkling of the plate decreases more significantly with the increase of the crimping force. In the forming process of this stainless steel sink, the risk of destabilization and wrinkling is most influenced by the friction factor, followed by the crimping force and least influenced by the radius of the concave die, which is also consistent with the results of the orthogonal test.
According to the results of the orthogonal test, it was determined that the influence of each factor in descending order is friction factor, crimping force, and radius of concave mold corner, and the optimal combination of molding process parameters for the part is R1C4F4, i.e., the radius of concave mold corner is 5 mm, the friction factor is 0.2, and the crimping force is 50 kN.
Final optimization results
Using the process parameters obtained from the orthogonal test results to optimize the design of the part drawing die, and re-use Dynaform software to simulate the drawing of the part forming, and get the forming limit diagram. It can be seen that the forming effect is better in the bottom forming area of the part, and the closer the side wall part of the part is to the flange, the more obvious the tendency of wrinkling is, and the flange part of the part has a certain degree of wrinkling problem, and the wrinkling problem of the flange part of the sink in actual production can be solved by cutting edge processing. Therefore, the forming limit diagram of stainless steel sink shows that the SS304 stainless steel sink destabilization wrinkling problem is solved.
Learn more about the Everything you need to know about SUS SS304.
Are there any alternative stainless steel grades that can be used to produce sinks?
While grades 304 and 316 are the most common stainless steel materials used in sink production, other options include:
Grade 201 stainless steel: This material offers a lower cost option, but it may not be as corrosion-resistant as 304 or 316 stainless steel. It is suitable for areas with low exposure to corrosive substances.
Grade 430 stainless steel: This is a ferritic stainless steel with good corrosion resistance and is typically more affordable than the 300 series. However, it is not as resistant to stress corrosion cracking or pitting as 304 or 316 stainless steel.
Learn more about the A Complete Guide to Stainless Steel AISI 420
What factors should be considered when selecting the thickness of the stainless steel sink material?
The Benefits of Using 0.05mm 304 Stainless Steel Foil in Your Application
What are some additional production techniques used to create high-quality stainless steel sinks?
301 Stainless Steel Foil: Production, Application, and Packaging
How can you ensure the quality of the stainless steel sink material during production?
Learn more about the 25 Years of Half-Hard 304 Stainless Steel Coil Manufacturer
How can consumers choose the right stainless steel sink material for their needs?
Consumers should consider the following factors when selecting the ideal stainless steel sink material for their needs:
Budget: Determine your budget, and choose a stainless steel grade and thickness that fits within your price range while still providing the desired level of quality and durability.
Corrosion resistance: If you live in an area with high humidity or use harsh cleaning chemicals, opt for a stainless steel material with superior corrosion resistance, such as grade 316.
Appearance: Consider the visual appeal of various finishes and textures when selecting a stainless steel sink material, as this can impact the overall aesthetic of your kitchen.
Maintenance: Choose a stainless steel sink material that is easy to clean and maintain, such as grade 304, which is known for its resistance to staining and tarnishing.
Warranty: Look for sinks that come with a warranty from the manufacturer, as this provides assurance of the sink’s quality and durability.
Conclusion
Based on the finite element software Dynaform, the influence of three process parameters such as the radius of the concave die fillet, the friction factor and the crimping force on the maximum thickening rate of the SS304 stainless steel sink deep-drawing formed parts was studied by the orthogonal test method. The optimum forming process parameters for SS304 stainless steel sink were obtained as R1C4F4, i.e., the radius of concave die fillet was 5 mm, the friction factor was 0.2, and the crimping force was 50 kN. The optimization results were used to redesign the deep drawing die so that the problem of instability and wrinkling of the part could be solved.
Selecting the ideal stainless steel sink material is crucial for ensuring the long-term performance, durability, and ease of maintenance of your kitchen sink. By understanding the various stainless steel grades, production techniques, and factors to consider when choosing the appropriate material, you can make an informed decision and invest in a stainless steel kitchen sink that will stand the test of time.
Yaoyi, a family-owned stainless steel manufacturer, with 28+ years of experience. Get the best solution for stainless steel coils with us.